Injection molding services are the backbone of the plastic parts production industry. They offer a comprehensive solution for transforming raw plastic materials into a wide variety of finished products.
The injection molding process starts with the selection of the appropriate plastic material. There are numerous types of plastics available, each with its own unique set of properties. Commonly used plastics include polyethylene (PE), polypropylene (PP), polystyrene (PS), and polyvinyl chloride (PVC). Engineering plastics such as polycarbonate (PC), acrylonitrile - butadiene - styrene (ABS), and nylon are also widely used for their enhanced mechanical, thermal, and chemical properties. The choice of plastic depends on factors such as the required strength, flexibility, heat resistance, and chemical resistance of the final product.
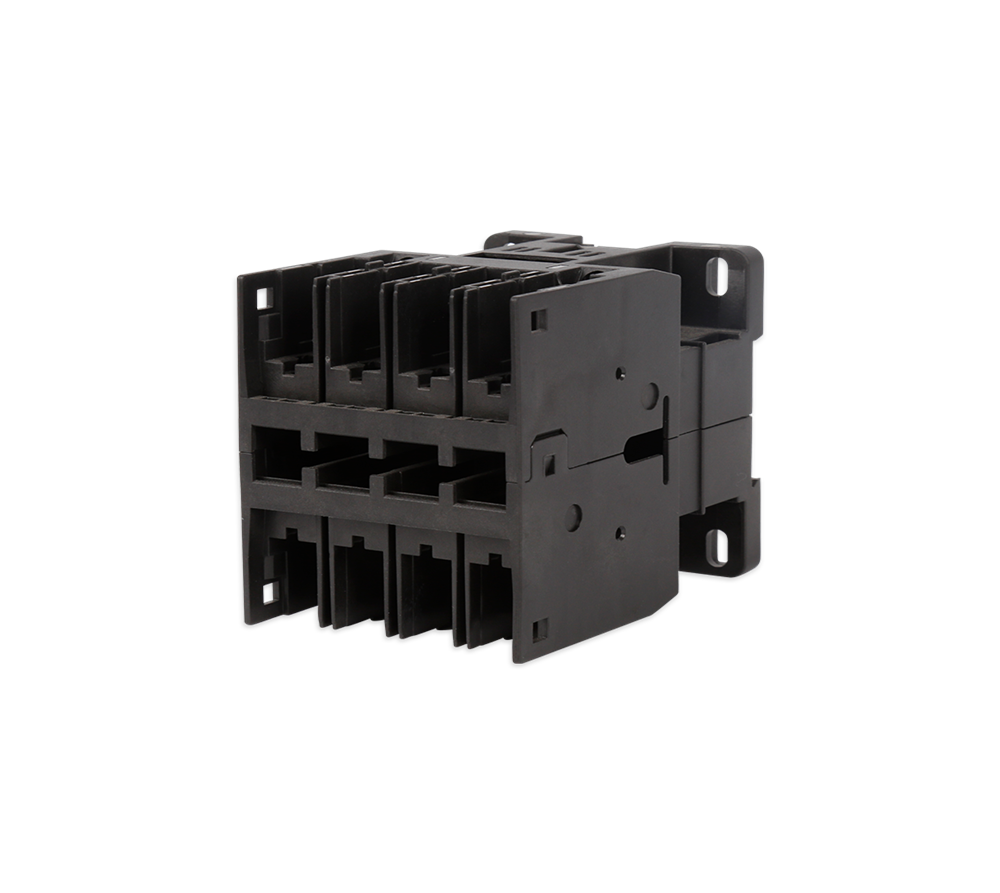
The injection molding machine is the core equipment in this service. These machines consist of several main components, including the injection unit, the clamping unit, and the mold. The injection unit is responsible for melting the plastic pellets and injecting the molten plastic into the mold. It consists of a hopper, a barrel, a screw, and a nozzle. The clamping unit holds the mold halves together during the injection and cooling process. The force exerted by the clamping unit must be sufficient to keep the mold closed against the pressure of the injected plastic.
The mold, which is typically provided by a plastic mold manufacturer, is the key to shaping the plastic into the desired form. As discussed earlier, molds can range from simple single - cavity molds to complex multi - cavity or family molds. The quality and design of the mold have a direct impact on the quality and production efficiency of the molded parts.
During the injection molding process, the plastic pellets are first fed into the hopper. From the hopper, they are conveyed into the barrel, where they are heated and melted by the rotation of the screw. The molten plastic is then forced through the nozzle and into the mold cavity. The injection pressure and speed are carefully controlled to ensure that the molten plastic fills the mold cavity evenly and completely. Once the mold is filled, the plastic is allowed to cool and solidify. The cooling time depends on factors such as the thickness and geometry of the part and the type of plastic used.
After the plastic has solidified, the mold is opened, and the molded part is ejected. The ejection mechanism must be designed to avoid damaging the part. This may involve the use of ejector pins, sleeves, or other ejection devices. The entire injection molding cycle, from injection to ejection, can be completed in a matter of seconds to minutes, depending on the complexity and size of the part.
Injection molding services offer several advantages. One of the main advantages is the ability to produce complex shapes with high precision. The molds can be designed with intricate details such as threads, undercuts, and thin walls. This allows for the production of parts that would be difficult or impossible to manufacture using other methods. Another advantage is the high production rate. Once the process is set up and optimized, large quantities of parts can be produced in a short period of time, making injection molding ideal for high - volume production.
Quality control is a crucial aspect of injection molding services. During the production process, various parameters such as temperature, pressure, and cycle time are monitored to ensure that the parts are being produced within the specified tolerances. Visual inspections are carried out to check for surface defects such as scratches, sink marks, or warping. Dimension checks are performed using measuring tools such as calipers, micrometers, or CMMs to ensure that the parts meet the design requirements.
Injection molding services can also be customized to meet specific customer requirements. This may involve adding inserts or performing secondary operations such as painting, plating, or assembly. Inserts can be made of metal, glass, or other materials and are used to add additional functionality or strength to the plastic part. Secondary operations can enhance the aesthetic or functional properties of the part.
In conclusion, injection molding services provide a reliable, efficient, and versatile solution for the production of plastic parts. Their ability to work with a wide range of plastics, produce complex shapes, and achieve high production rates makes them an essential part of many industries. By ensuring strict quality control and offering customization options, they can meet the diverse needs of their customers and deliver high - quality plastic products.